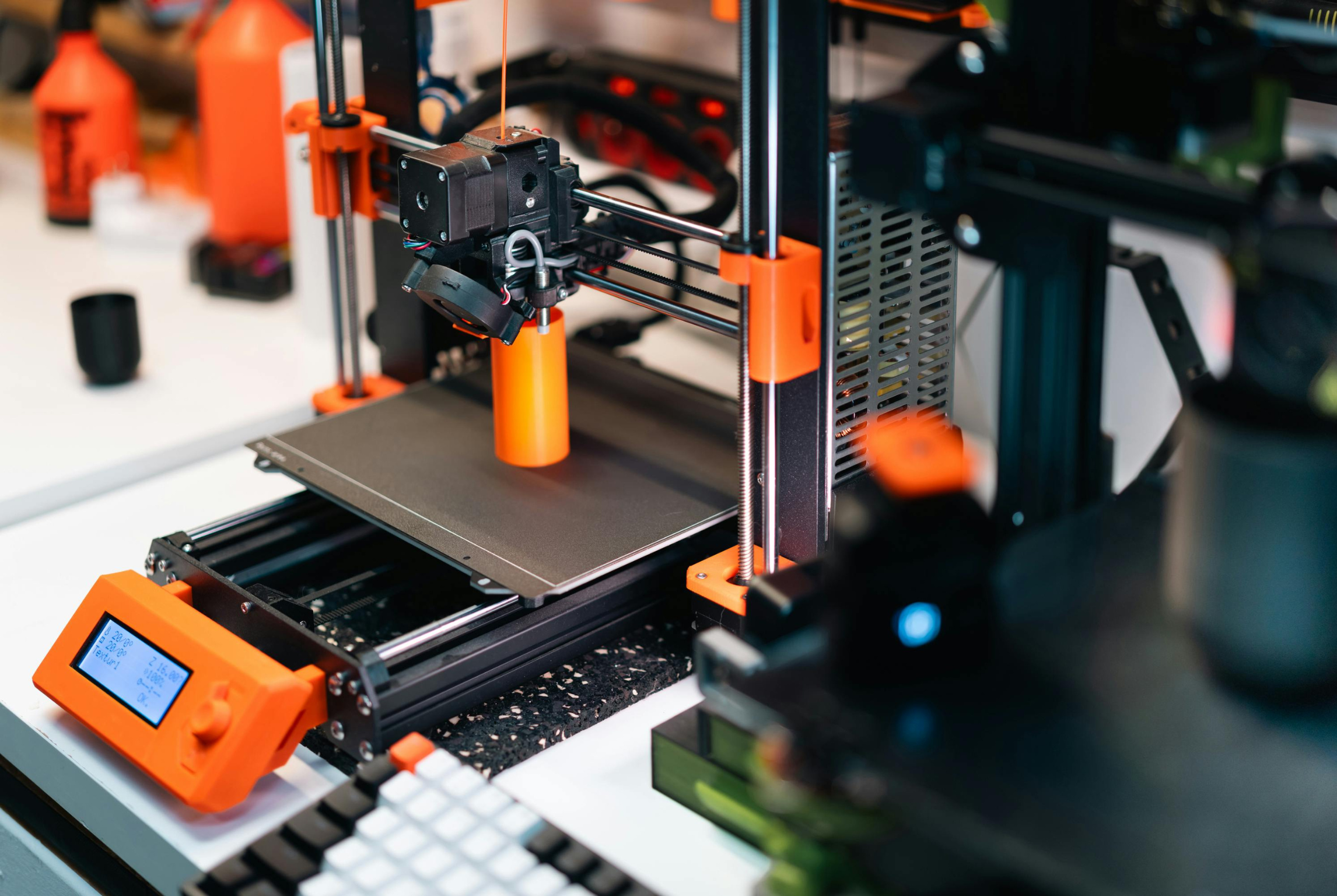
You’re printing a drone part, spending hours on modeling, getting that perfect layer, and then the first launch... but the casing deforms from the heat of the motor. Or you try to make a kitchen accessory meant to withstand the temperature of a hot pan, only for it to melt at the first use. Sound familiar?
These moments highlight a crucial lesson: it’s not just about knowing how to print but also about choosing the right material. Especially when it comes to projects that require withstanding high temperatures. If you’re passionate about 3D printing and want to create not just beautiful but functional objects, this guide will walk you through heat-resistant filaments. We’ll explore which materials won’t melt, where to use them, and how to select the right one to ensure your models last longer and perform better.
Understanding Heat Resistance in 3D Printing
To confidently choose the right materials for 3D printing, especially if the parts will be exposed to high temperatures, it is essential to understand what makes a filament heat-resistant. The answer lies not in a single number but in a range of characteristics that are often overlooked, even by seasoned makers.
Glass Transition, Heat Deflection, and Melting Points — Key Parameters
First and foremost, it’s crucial to consider the Glass Transition Temperature (Tg). This is the point at which the plastic softens and begins to lose its shape and strength, even though it may still look intact. This is when the material becomes vulnerable, so understanding this temperature is essential.
Next, there is the Heat Deflection Temperature (HDT), which indicates the temperature at which the material begins to deform under stress. This is especially important when your part will be exposed to real-world conditions like sitting in a hot car, near a stove, or inside electronics enclosures. A high Tg doesn’t guarantee durability if the HDT is too low.
Finally, we come to the Melting Point, which is when the material turns into a liquid. While important, this is not always the primary focus. Why? Because your model is more likely to lose its shape from heat before it actually melts.
If you’re planning to print something that needs to perform, not just look good on the shelf, don’t just check the "maximum temperature" on the filament package. Look for information about HDT, especially if you're printing functional parts. This will determine whether your project can handle the heat or if it will deform when exposed to really high temperatures.
Heat-Resistant Filaments
When it comes to heat-resistant filaments, there are several options to choose from, each with its unique set of characteristics. For those looking for the best heat-resistant filament, here are a few noteworthy choices:
-
PETG Heat Resistance: PETG is widely known for its excellent balance of printability and heat resistance. While not as heat-resistant as some other materials, it performs well for projects that don’t require extreme temperatures.
-
PLA Heat Resistance: PLA has a deformation temperature of about 60°C-70°C, meaning it will start to lose its shape in moderately hot environments. However, heat-resistant PLA has been developed to overcome this limitation.
-
Heat-Resistant Resin: Resin-based filaments also offer heat resistance, ideal for printing parts that will be exposed to relatively high temperatures without deforming.
-
ABS Heat Resistance: ABS is a popular choice for printing parts that need to resist heat, with an HDT of around 100-110°C. Though not as high as some other options, it is still commonly used for prototyping and consumer products.
For higher temperature needs, consider high-temperature filament options like PEEK and Ultem, which are designed for high-temperature 3D printing applications. These filaments can withstand temperatures exceeding 200°C, making them ideal for use in aerospace, automotive, and medical applications.
Choosing the best filament for heat resistance involves understanding your project’s specific needs. Whether you're looking for high-temperature 3D printer filament, high-heat-resistant filament, or a more specific solution like high-temperature nylon filament, always check for compatibility with your printer and the material's specific temperature limits.
Top Heat-Resistant Filaments – Which to Choose So Only the Idea Melts, Not the Part?
When your projects go beyond decorative figurines and move into real engineering, like kitchens, cars, or electronics, standard PLA just won’t cut it anymore. You need the heavyweights. Below, we’ll briefly explain which filaments can withstand extreme temperatures and won’t let you down in the hottest conditions.
PEEK (Polyether Ether Ketone) – The King of Engineering Filaments
If you want to print like NASA, PEEK is your material. This super polymer offers incredible heat resistance and strength, making it widely used in aerospace, medical, and industrial engineering applications.
-
Tg: 143°C
-
HDT: 260°C
-
Melting Point: 343°C
Pros:
-
Maximum resistance to temperature, chemicals, and load
-
Ultra-durable for real-world use
Cons:
-
Very expensive
-
Requires a printer with an extruder up to 400°C and a sealed chamber
Use for parts in aviation, automotive, medical implants, and critical mechanical components.
Ultem (PEI – Polyetherimide) – Industrial Standard for High-Temperature Printing
If you need a balance between strength, stability, and availability, Ultem is the perfect middle ground. It’s commonly used in the automotive and medical industries.
-
Tg: 217°C
-
HDT: 170–210°C
Pros:
-
Lightweight, strong, fire-resistant
-
Resistant to chemicals and sterilization
Cons:
-
Still requires a high-temperature printer
-
Can be expensive for hobby printing, but cheaper than PEEK
Often used in aviation panels, medical enclosures, and automotive parts.
Polycarbonate (PC) – Impact-Resistant and Transparent Like Bulletproof Glass
PC is the favorite for those seeking impact resistance and good heat resistance. It’s ideal for functional parts that must withstand both pressure and heat.
-
Tg: 147°C
-
HDT: 130–150°C
Pros:
-
High strength and impact resistance
-
Partially transparent
-
Suitable for functional parts
Cons:
-
Tends to deform during printing, especially without an enclosed chamber
-
Requires precise calibration
ABS (Acrylonitrile Butadiene Styrene) – The Proven Classic for Reliability Enthusiasts
If you're just starting to print functional parts, ABS is a step up from PLA. It’s chosen for its affordability, strength, and heat resistance, though it’s a bit tricky to print.
-
Tg: 105°C
-
HDT: 100–110°C
Pros:
-
Good mechanical properties
Affordable
Suitable for prototypes that can be post-processed
Cons:
-
Emits fumes — ventilation needed
-
Can crack without a heated bed and chamber
Applications: Gadget enclosures, household items, prototypes.
PETG (Polyethylene Terephthalate Glycol) – The All-Rounder with Moderate Heat Resistance
PETG is an excellent choice for a smooth transition into durable, moisture-resistant materials. It works well for outdoor and kitchen projects, but be careful — it doesn’t like overheating.
-
Tg: 80°C
-
HDT: 65–80°C
Pros:
-
Easy to print
-
Excellent layer adhesion
-
Moisture-resistant
Cons:
-
Not suitable for all tasks — starts to deform at temperatures above 70–80°C
PETG Heat Resistance makes this filament a popular choice, but it's important to consider PLA heat resistance for projects where the material won’t be exposed to high temperatures. While PETG offers better heat resistance than PLA, it’s still not a solution for extreme heat. If you need something even more durable, ABS heat resistance or heat-resistant resin might be your best options. Heat-resistant PLA and resin are suitable for moderately heated environments. The melting point of PLA filament is around 180°C, which is why it's not ideal for high-temp applications, whereas polyethylene's heat resistance can sometimes provide more reliable durability.
📊 Comparative Overview
Filament |
Tg (°C) |
HDT (°C) |
Ease of Printing |
Ideal For |
PEEK |
143 |
>260 |
Difficult |
High-performance engineering |
Ultem |
217 |
170–210 |
Moderate |
Aerospace, automotive |
PC |
147 |
130–150 |
Moderate |
Functional prototypes |
ABS |
105 |
100–110 |
Easy |
General-purpose parts |
PETG |
80 |
65–80 |
Very Easy |
Everyday items |
What Can Your 3D Printer Handle If You Are Venturing Into High-Temperature Projects?
When it comes to heat-resistant filaments, it’s not only about the materials but also about the technical specifications of your printer. You can buy the top-tier PEEK filament, but without the right equipment, it will just sit on your shelf as a luxurious decoration.
If you're seriously considering upgrading from hobby printing to professional engineering, ensure your printer can handle these advanced filaments. Below are the specifications your printer needs to handle filaments that won’t melt at the first hint of heat:
Extruder Temperature: Up to 400°C – Not a Joke
For PEEK and Ultem, the print head temperature should reach up to 380–400°C. For polycarbonate (PC), the temperature should range from 250 to 300°C. Most standard home printers, such as the Ender 3 or Prusa i3, are not designed to handle these temperatures without significant upgrades.
What Can You Do?
1. Replace the hotend with a true "all-metal" one.
2. Install a heat-resistant Teflon tube.
3. Check the thermistor and heating block (PID calibration will help).
Heated Bed: The Antidote to Warping
Heat-resistant materials, especially ABS and PC, tend to "lift" their corners and detach from the platform. The solution is a properly set-up and stable heated bed:
ABS: 90–110°C
PC: 100–120°C
Ultem/PEEK: Up to 140°C
Uniform heating and correct adhesion (e.g., using a stick glue or specialized sprays like Magigoo) make a significant difference.
Our Tip: Use a PEI surface or glass + glue, and disable the first layer cooling — heat must stay.
Your Secret Ingredient: Closed Chamber
Perhaps the most underrated yet critical condition for successful printing is controlling the surrounding temperature. This is especially important for PC and ABS, which are sensitive to drafts, temperature fluctuations, and the "freezing" of the second layer.
Why It’s Important?
1. Prevents cracking and delamination.
2. Improves layer adhesion.
3. Ensures consistent temperature throughout the part.
If your model is large and functional, a closed chamber or, at the very least, a DIY acrylic cover with a thermometer inside is a must-have.
What We Recommend:
✅ Not every printer can handle high-temperature printing, but nearly all can be upgraded step by step.
✅ First, check if your model can handle the required temperature, then spend money on expensive filaments.
✅ Don’t forget basic thermal stability: every degree matters.
How to Avoid Common Mistakes When Printing with Heat-Resistant Filaments
Even if you’ve got a top-tier spool of Ultem and your printer is ready to handle 350 °C, printing with heat-resistant materials can still go wrong. Many beginners — and even experienced users — often overlook issues that can ruin a print at the final stage. Let’s explore how to avoid the most common problems and ensure successful results.
1. Warping: When Your Model Starts Lifting at the Corners
This is one of the most common issues encountered when printing with high-temperature filaments. It often happens with ABS, PC, and PEEK. Everything seems fine at the start, but after 30 minutes, the model's corners begin to lift, and you may have to restart the entire print.
Why does this happen?
Uneven cooling causes the material to shrink and pull itself upward. Without stable heat and proper adhesion to the print bed, layers can separate.
What can you do?
1. Use an enclosed chamber or build a simple box from acrylic sheets.
2. Set the heated bed to 90–120 °C, depending on the material.
3. Apply adhesives like Magigoo HT, glue stick, Kapton tape, or BuildTak.
4. Print the first few layers slowly and without fan cooling.
Our pro tip: Preheat your bed for 10 minutes before printing — it helps stabilize the surface temperature.
2. Moisture: The Hidden Enemy of Print Quality
Many filaments, such as nylon, PETG, and even PC, absorb moisture from the air. Moisture leads to bubbles, sizzling sounds during printing, poor layer adhesion, and a spongy final result.
How to recognize it?
You hear a crackling noise, see bubbles in the nozzle, or find pits on the print’s surface.
How to avoid it?
1. Store your spools in airtight boxes with silica gel
2. Use filament dryers like eSUN eBox, SUNLU, or even a kitchen oven at 60–70 °C
3. Print directly from a heated dry box (options available from Polymaker or PrintDry)
Keep in mind that PETG can absorb up to 0.2% of its weight in water within 24 hours, which impacts model strength and print stability.
3. Harmful Fumes: Print Safely and Breathe Easy
Some filaments, like ABS, ASA, and PEEK, emit fumes such as styrene, which may cause health issues if inhaled over time.
What you should do:
1. Ventilate your workspace or use an exhaust fan
2. Ideally, use printers with HEPA and carbon filters (e.g., Bambu Lab or Raise3D)
3. Avoid printing in sleeping or kitchen areas — even if your ventilation is good
Styrene, which is released by ABS during printing, is listed as a possible carcinogen by the EPA. Don’t take chances with your health.
Use This Cheat Sheet
Problem |
Solution |
Warping |
Enclosed chamber, heated bed, adhesives, and correct first layer speed |
Moisture in Filament |
Use filament dryers, airtight containers, and print from a heated dry box |
Harmful Fumes |
Ventilation, air filters, open windows, print in a separate, safe area |
How Heat-Resistant Filaments Are Used
When we talk about heat-resistant filaments, materials like Ultem, PEEK, and PC are not just new tech trends for 3D printing fans — they are real solutions for industry. We have seen a rise in the popularity of these high-temperature plastics and have tracked their use in various sectors. Their main advantages are durability, resistance to extreme conditions, and safety. Check the industries below to see how these filaments make a difference.
Automotive Industry: Where Every Detail Matters
Imagine you are under the hood of a sports car, where the temperature can easily go over 200°C. Any part that can’t handle this heat may fail. Ultem (PEI) comes to the rescue, offering heat resistance and strength. It is used to make engine components, such as sensor housings and air ducts, that must withstand high temperatures and sudden climate changes.
How does it work?
Ultem is perfect for this kind of task because it is not only strong but also flame-resistant, which is critical when operating in high-temperature conditions. Its resistance to chemicals also makes it ideal for car systems that contain aggressive fluids like oils and coolants.
In 2020, automotive companies started using 3D printing with Ultem to create lightweight, heat-resistant parts. This helped lower production costs and improve performance.
From Sterile Tools to Innovative Implants in Medicine
In healthcare, it’s more than just a trend. PEEK is a material used in the most critical areas of medicine, for example, to manufacture surgical tools and implants, such as artificial joints and dental crowns.
Why Is PEEK the Ideal Choice?
This filament resists chemical exposure and is biocompatible. This means it won’t be rejected by the body, making it ideal for implants that need to remain safe and sterile within the human body for an extended period.
Modern surgical tools made from PEEK can be sterilized, which is key for preventing infections and complications during surgery. It also allows the creation of personalized implants that fit the patient exactly.
Consumer Electronics
Now let’s talk about your smartphone or tablet. How often do they get dropped or hit? To protect devices from external damage, manufacturers are now using polycarbonate (PC) for their housings.
Polycarbonate is robust and impact-resistant. It is used to create plastic housings that can handle heavy shocks while keeping excellent optical clarity. This is especially important for screens, which are also often made from polycarbonate to provide a perfect balance of weight, strength, and transparency.
Tip for Engineers: Utilizing polycarbonate in consumer electronics helps reduce the device's total weight while still offering high impact resistance. It’s perfect for phones, tablets, and other gadgets that go through daily wear and tear.