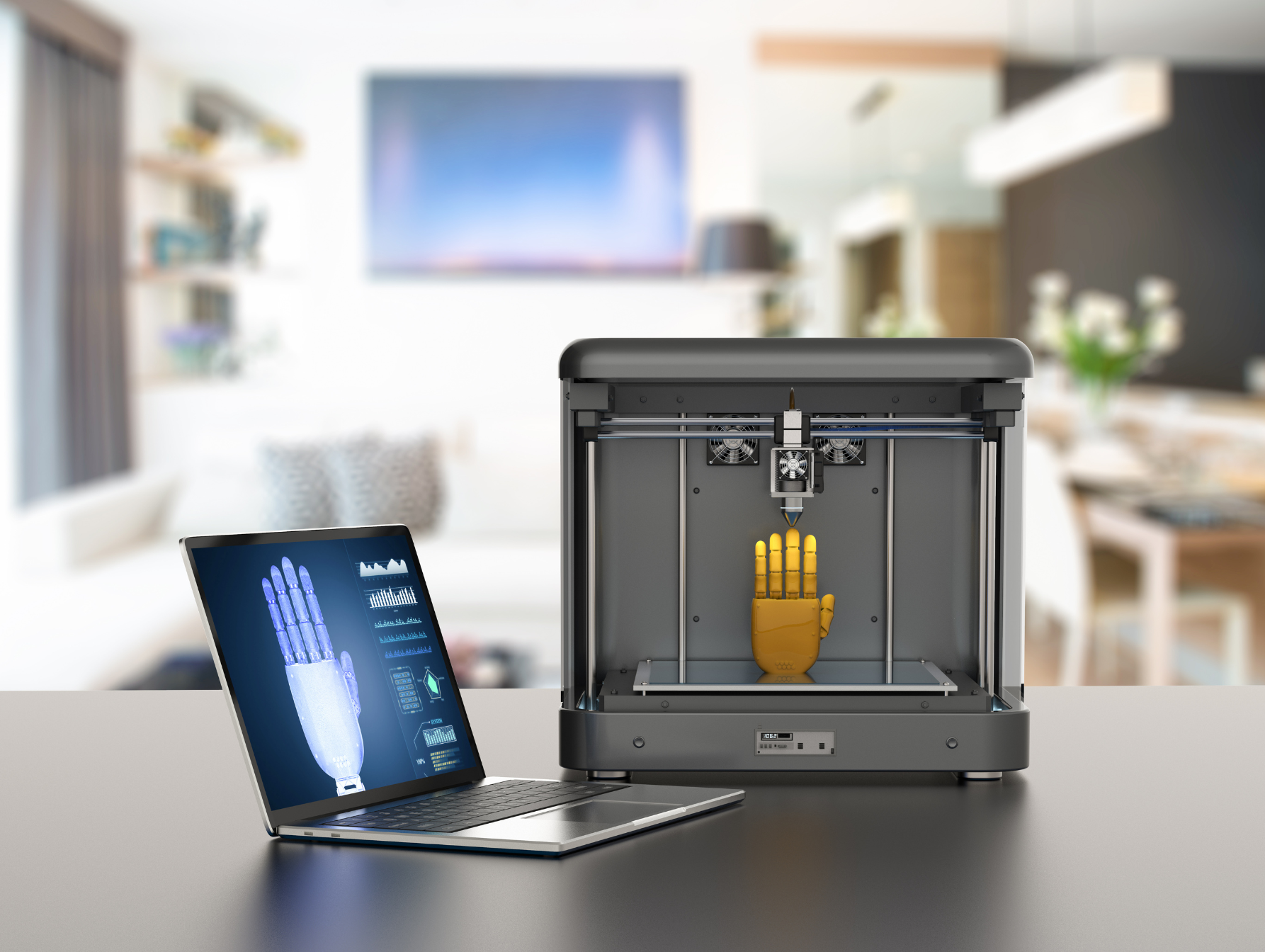
Have you ever found the perfect 3D model — maybe a figurine of your favorite character, a custom bike part, or a prototype for your startup? You’re ready to hit “Print”... but then comes the big question: what should you print it with? FDM? Resin? SLS? Or are they all basically the same thing?
If you’ve ever tried to choose a 3D printer or thought about ordering a printed model, you probably know that slightly confused feeling. At first glance, these technologies seem similar but in practice, the differences can be very important. Sometimes you need high detail, sometimes strength is the priority, and sometimes it’s all about convenience and budget.
We’ll break it all down for you: what FDM, SLA, and SLS mean, how they work, where they’re used, and most importantly, how to choose the right one for your needs. It’ll be clear and beginner-friendly, with real-life examples, pros, and cons.
So if you don’t just want to “print something,” but want to understand what you’re choosing, keep reading.
Technology Overview: FDM, Resin (SLA/DLP), SLS
At first, all those letters can seem confusing. But let’s look at it with simple examples. Imagine walking into a workshop with three different printers.
One of them works like a glue gun, slowly laying down melted plastic along a set path. Another looks like a mini science lab, turning liquid into solid using light. And the third one feels like something from a sci-fi movie; it uses a laser to fuse powder into complex shapes, right out of “dust.”
The three main 3D printing technologies are FDM, Resin (SLA/DLP), and SLS. Each one builds objects differently and has its own strengths and weaknesses. If you want to choose the best option for your project — miniatures, mechanical parts, or custom accessories — it’s essential to know what each system is really about.
The table below gives a quick summary you can use as a cheat sheet. Then, we’ll go through each technology step by step.
Technology |
How It Works |
Materials |
Advantages |
Limitations |
FDM (Fused Deposition Modeling) |
Melts and extrudes thermoplastic material |
PLA, ABS, PETG, TPU, etc. |
Affordable, easy to use, wide choice of materials |
Lower detail, visible layer lines |
Resin (SLA/DLP) |
Cures liquid resin with light |
Photopolymer resins |
High detail, smooth surface |
Needs post-processing, resin can be toxic |
SLS (Selective Laser Sintering) |
Laser fuses powder layer by layer |
Nylon, glass-filled materials |
Strong parts, no supports needed, complex geometry possible |
Expensive, requires more maintenance |
In the following sections, we’ll dive into how each technology works, what materials they use, and where their real superpowers shine.
Resin Printing
People unfamiliar with 3D printing are often very surprised when they unpack a figurine printed with a resin printer. No layers, no roughness — just a smooth, detailed surface that looks more like a cast item than something 3D-printed. It almost feels like science fiction.
That’s the magic of resin printing. It doesn’t use plastic filament like FDM printers — it uses light and liquid resin. A tray filled with resin, UV light, and incredible precision down to microns. The result? A quality that FDM simply can’t reach. Resin printing is especially great for miniatures, jewelry, medical models — anything that needs high detail and smooth finishes.
Are you ready to see why so many hobbyists, designers, and professionals fall in love with resin printing after the first print? Let’s go 👇
What makes resin printing so great?
1. Insane level of detail
If you want to print a tiny figure, resin printing can show every wrinkle on the face or pattern on a ring as if it was hand-carved. Some printers can reach 25-micron resolution — enough to reproduce tiny parts in medical prototypes, jewelry, or tabletop games. If you’ve ever held a resin miniature, you know the feeling — it looks almost alive.
2. Perfectly smooth surface
Forget sanding and polishing. Models printed with resin come out with a surface so smooth you can paint them right away. That’s super useful when you need a professional, aesthetic look — for example, in art projects or collector’s items.
3. Compact machines, high precision
You don’t need a huge printer to get amazing results. Even small desktop resin printers, like the Anycubic Photon or Elegoo Mars, can deliver pro-level quality. That makes resin printing suitable even for home workshops or small studios.
But there are some downsides too
1. Post-processing is a must
Printing is only the first step. After you take the model out of the resin vat, you need to wash it in isopropyl alcohol, dry it, and cure it under UV light. Otherwise, the model will stay sticky and won’t be strong enough. This adds a bit of "alchemy" to the process and requires care and time.
2. Smell and toxicity
Resin has a strong smell and can irritate your skin or lungs. That’s why you should always print in a well-ventilated space and use gloves, a mask, and safety glasses. If you’ve only worked with FDM before, this might come as a surprise.
💸 Resin cost
Good photopolymer resin isn’t cheap — it usually costs between $30 and $100 per liter, depending on the brand and type. That’s more expensive than standard filament like PLA or PETG. But the result is worth the price if you want high detail and a polished look.
What is resin printing best for?
1. Jewelry and dental models
If you once dreamed of being a dentist but chose another path, now you have a chance to get into this field without a medical degree. Thanks to resin printing, you can support dentists with modern tech and precise models. Both jewelry and dental industries require micron-level precision, and resin is perfect for that. Whether it’s a ring or a dental crown, you’ll get a result like the CAD file.
2. Tabletop miniatures
For fans of DnD, wargames, or figure collectors, resin printing opens the door to a new level of detail and artistic quality. With clean lines and sharp textures, you’ll impress your audience.
3. Artistic and creative projects
If you’re a sculptor, designer, or love making unique things, a resin printer gives you complete creative freedom. Nothing is holding you back.
SLS (Selective Laser Sintering)
Heavy-duty printing for engineers and small-scale manufacturers
SLS printing is the solution when you need more than just a nice shape, strength, durability, and real functionality. This technology goes beyond hobby projects or prototypes and moves into engineering and small-batch production. A laser fuses powder particles together into solid, strong parts with high precision, without needing any supports.
The result?
A functional part that’s almost ready to use straight out of the printer.
Each 3D printing method plays its role. FDM is for drafts, Resin is for display, and SLS is the workhorse — it creates complex parts ready for real work. Let’s dive into why engineers across the globe rely on SLS and what you should know before starting.
What makes SLS printing great?
-
No supports = no design limits
One of the biggest advantages of SLS is the ability to print complex shapes without any supports. The part is formed inside a powder bed, like it’s cradled in a soft cushion that holds its shape during printing. This opens up endless possibilities for creative and functional design, without worrying about sagging or breaking during the process.
-
High strength – proven in real use
Parts printed with nylon or glass-filled materials using SLS can handle real mechanical stress. They’re perfect for devices that experience pressure, heat, or movement. This technology is often used for working prototypes, spare parts, or components close to final production quality.
-
Ideal for small-batch production and engineering
SLS becomes a key tool when you need to make multiple identical or slightly customized parts. You can print dozens of items in a single run by packing them efficiently in the build chamber. Engineers love the time savings and the ability to make production-ready models instantly.
What are the downsides?
1. Cost is still high
Full-size SLS printers cost tens of thousands of dollars. Materials and maintenance also come with a serious price tag. However, more affordable desktop versions are becoming available, making SLS more accessible for small businesses and labs.
2. Post-processing takes time
After printing, you must clean the part thoroughly to remove any leftover powder. Depending on the final use, you may also need to sand or paint it. This process takes time and requires a dedicated space with dust protection, proper ventilation, and a separate area for finishing. Still, the results are worth the effort.
3. Maintenance is close to industrial level
An SLS printer requires good ventilation, air filtration, temperature control, and a clean printing environment. It’s not a desktop toy — it’s a serious piece of equipment that needs regular maintenance and a careful setup.
How can you use SLS printing?
-
For real product testing
If you're testing a product before mass production, SLS allows you to make a working model that functions under real conditions, not just something that looks good.
-
For high-stress parts
Gears, mounts, enclosures, and other components that face physical stress can be printed with SLS. They’re strong, durable, and suitable for actual use.
-
For low-volume industrial production
If mass production isn’t practical but you still need 20, 50, or 100 pieces, SLS is the perfect solution. It’s fast, flexible, and doesn’t require expensive molds or tools.
How to Choose the Right 3D Printer for Your Needs
We’ve covered a lot about different types of 3D printers, but if you’re still wondering, “How do I choose the right 3D printer for my needs?”, let’s sum it up and answer your question clearly:
Choose FDM if…
...you’re a beginner or enthusiast who wants to print functional parts, prototypes, and everyday objects without spending too much or dealing with complicated setups.
FDM is a reliable workhorse, perfect for those who want to learn, experiment, and solve practical tasks — from phone holders to electronic enclosures. It’s simple, user-friendly, and budget-friendly. Even affordable models like the Creality Ender-3 or Anycubic Kobra can deliver solid results.
If you’ve heard about "resin vs filament 3D printer" and don’t know where to start, go with filament (FDM).
Choose Resin (SLA/DLP) if…
...you’re aiming for high detail and excellent visual quality. This technology is perfect for people who love tabletop games, jewelry making, dental modeling, or simply want their prints to look like small works of art.
Resin printers provide a smooth surface and micron-level precision that makes each model look factory-made.
Ideal for:
1. Miniatures, figurines, and sculptures
2. Jewelry molds
3. Medical and creative models
When comparing FDM vs Resin, remember: FDM is “strong and simple,” while Resin is “precise and beautiful.” Just keep in mind that Resin printing needs more care and safety measures.
Choose SLS if…
Your projects involve real functionality, stress resistance, complex geometry, or small batch production, and you want your printed part to work straight out of the box.
Thanks to support-free printing, strong materials, and high design freedom, SLS is the choice of professionals, engineers, and manufacturers.
Best for:
1. High-stress parts and gears
2. Casings and mechanical components
3. Small-scale production